The design and material of a CV joint cage play a crucial role in determining its durability and performance. The CV joint cage, also known as the race or retainer, is an essential component within a constant velocity (CV) joint. It holds the ball bearings or rollers in place, allowing for the smooth transfer of torque from the driveshaft to the wheels while accommodating the rotational movement of the joint.
Firstly, let's discuss the impact of design on the durability and performance of a CV joint cage. The design of the cage determines its ability to distribute and manage the forces and stresses experienced during operation. A well-designed CV joint cage should evenly distribute the load on the ball bearings or rollers, preventing excessive stress on any specific area. This reduces the risk of premature wear or failure.
One commonly used design for CV joint cages is the "window" or "pocket" design. This design features pockets or windows that hold the ball bearings or rollers in place. It allows for a larger contact area between the cage and the balls, distributing the load more effectively. This design helps to minimize friction and wear, resulting in improved durability and performance.
Another design consideration is the number of windows or pockets in the cage. The number of windows affects the smoothness of rotation and the distribution of forces. Cages with a higher number of windows tend to offer better performance due to improved load distribution and reduced friction. However, a higher number of windows may also increase the complexity and manufacturing cost of the cage.
Now, let's explore the impact of material selection on the durability and performance of a CV joint cage. The material used for the cage must possess specific characteristics such as strength, hardness, and wear resistance to withstand the demanding operating conditions.
Steel is the most commonly used material for CV joint cages due to its excellent strength and durability. High-grade steel alloys, such as chrome-molybdenum steel, are often employed to enhance the cage's performance. These alloys provide superior strength and hardness, allowing the cage to withstand the high rotational speeds and heavy loads associated with CV joint operation.
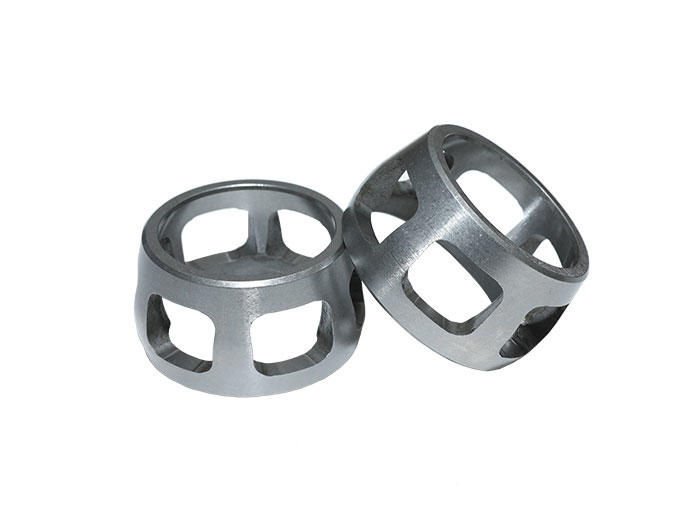
In addition to steel, some
CV joint cages may also incorporate other materials, such as polymers or composite materials. These alternative materials offer advantages like reduced weight, improved corrosion resistance, and reduced friction. However, their implementation is typically limited to specific applications or performance requirements.
It's worth noting that advancements in material science and manufacturing techniques have led to the development of innovative cage materials, such as carbon fiber-reinforced polymers or specialized coatings. These materials aim to further enhance the durability, performance, and longevity of CV joint cages.
In conclusion, the design and material of a CV joint cage have a significant impact on its durability and performance. A well-designed cage with an optimal number of windows and an appropriate material selection can effectively distribute loads, reduce friction, and minimize wear. Steel is the most common material due to its strength and durability, although alternative materials may offer specific advantages. Manufacturers continue to innovate in cage design and materials to enhance the performance and reliability of CV joints, ensuring smoother and more durable power transmission in automotive applications.